Comme nous l’avons vu dans les deux premiers épisodes de notre série d’articles « Rhino », les outils numériques ont largement été sollicités jusqu’ici et ils ont participé à modifier profondément le process et l’organisation de la production de chaussures orthopédiques sur mesure chez Breizh Podo.
Nous avons expliqué que le scan des pieds permet la création de formes auxquelles le podo-orthésiste apporte des corrections avant la modélisation du patronage. Par ailleurs, la conception et la fabrication des semelles orthopédiques (orthèses) suit elle aussi des étapes « numériques », comme nous avons pu l’expliquer dans un article précédent (La conception de nos semelles fait un bond géant) dès le mois de mai 2023 : scan des pieds, corrections et découpe de l’orthèse par une fraiseuse CNC.
Pour compléter l’ensemble des éléments qui ont été réunis jusqu’ici, il manque donc une pièce indispensable : l’orthèse.
Éliminer les contraintes et les pollutions de l’air
Avant l’intervention des outils numériques et la découpe de l’orthèse dans une plaque d’EVA (*) de 35 mm par une fraiseuse CNC, il fallait de multiples manipulations par un technicien pour réaliser cette pièce. « De façon traditionnelle, il fallait galber l’orthèse sur le moule. On collait couche après couche, de 3 mm, 5 mm ou 8 mm. Entre chaque couche, il fallait une épaisseur de colle et après avoir collé chaque épaisseur de matière, il fallait passer par le banc pour poncer. C’était fastidieux, il y avait une utilisation importante de colle et les passages au banc produisait de la poussière. Ce travail couche par couche générait donc beaucoup de manipulations et beaucoup de contraintes », explique Luc Sieurin. À la fin de cette opération relativement fastidieuse exclusivement réalisée à la main par les opérateurs de l’atelier, l’orthèse devait offrir une surface plate pour le contact au sol. La partie supérieure de la sole – ou semelle extérieure – venait donc s’adapter au-dessous de l’orthèse avec des ajustements pour obtenir la relève avant et le talon.
(*) EVA, de l’anglais ethylene vinyl acetate.
Des contraintes qui deviennent acceptables
Désormais, l’utilisation du logiciel de CAO (Conception assistée par ordinateur) Rhino (Rhinoceros 3D ou Rhino 8, logiciel de CAO développé par l’entreprise Robert McNeel & Associates) permet de fraiser un liège avec la hauteur de talon qui a été définie pour le patient, tout en respectant l’axe vertical pied-cheville. La seule limite que nous impose le fraisage d’un liège par une fraiseuse CNC, c’est une épaisseur de 35 mm puisque c’est l’épaisseur maximale des plaques d’EVA que nous pouvons utiliser.
« Si nous devons dépasser cette hauteur de 35 mm parce que nous avons besoin de plus de compensation, l’opérateur travaille alors le dessous de l’orthèse. Il s’agit de coller une épaisseur supplémentaire. L’opérateur trace sa ligne de repère et enlève ensuite l’excédent au banc. En général, quelle que soit la hauteur de l’orthèse finie (avec ou sans ajout de compensation), l’aplomb est bon ou alors il est obtenu à l’aide d’infimes retouches », commente Luc Sieurin.
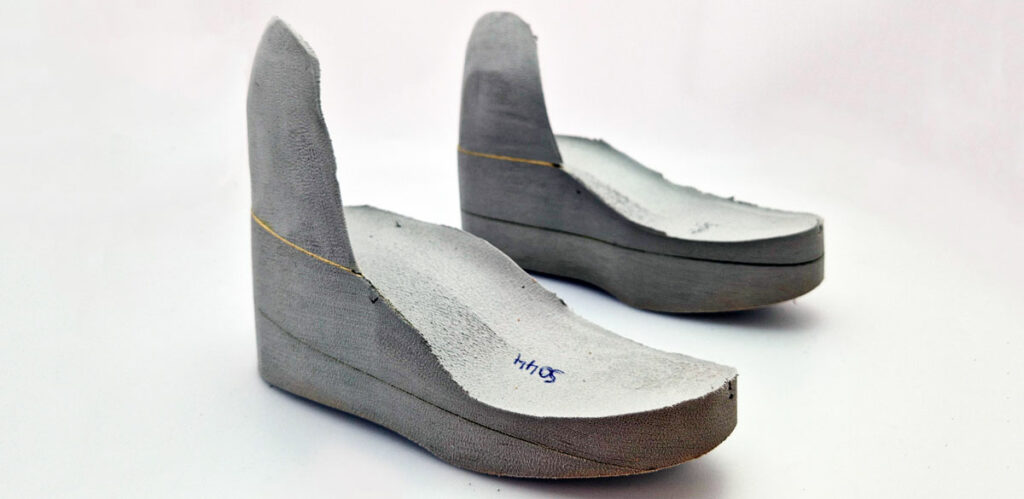
Du confort et du temps pour faire autre chose
Ainsi, l’orthèse n’est plus façonnée par couches successives collées et travaillées une à une au banc. L’orthèse est définie sur ordinateur, fraisée et simplement terminée au banc. Les opérateurs qui réalisent cette opération à l’atelier ont gagné en confort. Le temps consacré à ces tâches répétitives peut aussi être consacré à faire autre chose pendant que la fraiseuse se charge de découper le liège (EVA) avec une précision qui dépasse celle dont l’homme est capable. En effet, s’appuyer sur des outils numériques, c’est évoluer dans un cadre qui est sous contrôle et qui, pour une raison ou pour une autre, ne dévie pas. Sur le logiciel Rhino, l’opérateur travaille sur un calque millimétré qui lui offre des repères stables et d’une grande précision. Lorsque le fichier de découpe est envoyé à la fraiseuse CNC, cette étape de création numérique de l’orthèse est simple et précise et lorsque cette orthèse est découpée, elle ne nécessite plus qu’une finition rapide et minimale au banc.
De multiples avantages à la numérisation de la production en podo-orthésie
Avant d’évoquer dans un quatrième article (à venir : Rhinoceros 3D. Ep 4/4. Les projets, développements à venir) les évolutions que nous envisageons dans les mois et années à venir pour la production de chaussures orthopédiques sur mesure chez Breizh Podo, il est sans doute temps de dresser une liste des avantages relevés jusqu’ici.
Ainsi, la numérisation du process de production nous permet à ce jour de profiter de multiples avantages dans différents domaines.
Avantages pour les patients :
- Une prise d’empreinte (relevé numérique) beaucoup plus précise que le moulage traditionnel grâce au scan ;
- Il n’y a plus de perte d’informations sur les formes avec un procédé numérique ;
- L’impression 3D permet d’avoir des formes montantes et donc de conserver la précision dans la tige de la chaussure ;
- Il est possible d’imprimer une empreinte « virtuelle » en 3D avec une extrême précision, avec ou sans corrections ;
- Le résultat obtenu est tout de suite ajusté.
Avantages pour la production et l’entreprise :
- Il est possible d’apporter à l’empreinte numérique des corrections qui peuvent être annulées et/ou modifiées par la suite ;
- Nous obtenons des relevés de plan parfaits et surtout fiables.
- Nous pouvons nous appuyer sur un process dont chaque étape a été testée et validée. Nous avons la certitude d’obtenir de véritables avantages à chaque étape de la production ;
- Nous bénéficions au final de gains en efficacité, en productivité et donc en rentabilité.
Avantages pour les opérateurs :
- Les formes sont beaucoup plus légères et faciles à manipuler ;
- Il y a une importante réduction de la présence de solvants (résine, colle) et de poussières ;
- Ils réalisent beaucoup moins de tâches chronophages et répétitives.
Avantages environnementaux :
- Réduction de l’utilisation de produits volatils ;
- Réduction du dégagement de poussières ;
- Utilisation d’une matière recyclable pour l’impression des formes en 3D.
Aucun regrets et toujours autant d’envie d’innover
En réponse aux avantages listés ci-dessus, nous n’avons pas réellement trouvé d’inconvénients… Pourtant, une part d’esprit critique ne nous manque pas. Trois ans après avoir engagé notre mutation numérique, nous n’avons absolument aucun regret et nous devons même avouer que l’idée de ne pas avoir emprunté cette voie pourrait même nous faire peur… C’est donc avec de belles certitudes et beaucoup d’envie que nous envisageons l’avenir. Cet avenir, nous le concevons avec de nouvelles étapes, de nouvelles évolutions qui viendront enrichir, compléter et prolonger tout ce qui a été réalisé jusqu’ici. Pour conclure cette série de quatre articles consacrés à la numérisation chez Breizh Podo, nous vous proposons donc un article dans lequel nous évoquons l’avenir. Vous êtes prêts à nous suivre dans de nouvelles aventures ? Rendez-vous sur cette page : Rhinoceros 3D. Ep 4/4. Les projets, développements à venir.
Lire la suite :
Épisodes précédents :
Autres articles sur la numérisation du process de fabrication chez Breizh Podo :
- Breizh Podo, une entreprise hautement équipée (janvier 2022)
- L’impression 3D change tout pour nos patients (octobre 2022)
- Breizh Podo au cœur de la révolution numérique (novembre 2022)
- La conception de nos semelles fait un bond géant (mai 2023)