Depuis 2021, Breizh Podo a engagé une profonde mutation de sa production en intégrant de nouveaux process de fabrication qui s’appuient sur des outils numériques. Le logiciel de conception assistée par ordinateur (CAO) Rhinoceros 3D a peu à peu pris une place centrale au point d’être aujourd’hui indispensable. Nous vous proposons une série de quatre articles qui expliquent et racontent comment Rhino s’est imposé dans chaque étape de la conception et de la fabrication d’une chaussure orthopédique sur mesure.
Dans ce premier article, nous commençons par les formes, puis nous évoquerons le relevé de formes avant de nous intéresser aux orthèses dans le troisième article. Dans le quatrième article, nous évoquerons l’avenir. Car chez Breizh Podo, le futur est en marche !
Améliorer le process de production des formes
Entrer dans la réserve de Breizh Podo, c’est découvrir un espace unique où sont entreposées des centaines de formes. Les formes de montage servent à la confection d’une chaussure. Comme leur nom l’indique, ces moules ont la forme des pieds, puis elles intègrent les corrections apportées par le podo-orthésiste avant que les différentes pièces qui constituent la chaussure viennent trouver leur place sur cette forme. À l’origine, les formes étaient en bois, puis d’autres matériaux sont apparus, tels que la résine ou le plâtre.
Chez Breizh Podo, jusqu’à il y a quelques années, le process de confection d’une paire de chaussures orthopédiques prévoyait qu’un moulage soit fait des pieds de chaque patient. Puis une résine était coulée dans l’empreinte pour donner la forme. À cette forme, à ce moulage du pied, le rôle du podo-orthésiste consiste donc à apporter les corrections nécessaires. Très souvent, il s’agit d’apporter des zones de décharge nécessaire en ajoutant un ou plusieurs volumes. De la matière était donc ajoutée aux formes de départ. Une fois les corrections apportées, l’équipe de l’atelier créait la chaussure orthopédique qui était complétée par une semelle orthopédique (orthèse).
Améliorer le process de production des formes
Cette méthode de travail et cette façon de procéder sont les mêmes partout où est pratiquée la podo-orthésie. Chez Breizh Podo, il y a cependant eu plusieurs évolutions majeures liées à une phase de numérisation. Nous avons déjà eu l’occasion de partager des articles sur le sujet sur ce site :
- Breizh Podo, une entreprise hautement équipée (janvier 2022)
- L’impression 3D change tout pour nos patients (octobre 2022)
- Breizh Podo au cœur de la révolution numérique (novembre 2022)
- La conception de nos semelles fait un bond géant (mai 2023)
Cette modernisation du process n’a pas simplement été une volonté de suivre les évolutions technologiques ou une tendance à la numérisation que l’on connaît dans de nombreux domaines de notre monde moderne et dans les entreprises. Ce qui a motivé la réflexion et la mise en place d’un nouveau process repose sur un enchainement simple qui a été modernisé : le moulage des pieds du patient est remplacé par un scan des pieds, puis le fichier obtenu peut être modifié en apportant les corrections nécessaires avant d’imprimer la forme en 3D pour pouvoir créer la chaussure sur cette forme.
De nombreux avantages à l’impression 3D des formes
Chez Breizh Podo, les avantages concrets issus de cette numérisation du process de création et de fabrication des chaussures orthopédiques ont rapidement été perçus :
- Le scan, qui est un relevé numérique, est une prise d’empreinte beaucoup plus précise que le moulage traditionnel ;
- L’empreinte numérique peut recevoir aisément des corrections qui peuvent être annulées et/ou modifiées par la suite ;
- Avec ou sans corrections, l’empreinte « virtuelle » peut être imprimée en 3D avec une extrême précision ;
- Il n’y a aucune perte d’informations avec un procédé numérique (les moulages traditionnels étaient manipulés, corrigés et modifiés et généraient des pertes d’informations) ;
- La forme obtenue est beaucoup plus légère et facile à manipuler ;
- Le process optimisé et il évite aux équipes d’atelier de réaliser des tâches chronophages et répétitives ;
- Avec l’impression 3D, plus de résines et leurs solvants volatils qui se répandent dans les ateliers ;
- Enfin, la matière qui sert à l’impression 3D est recyclable.
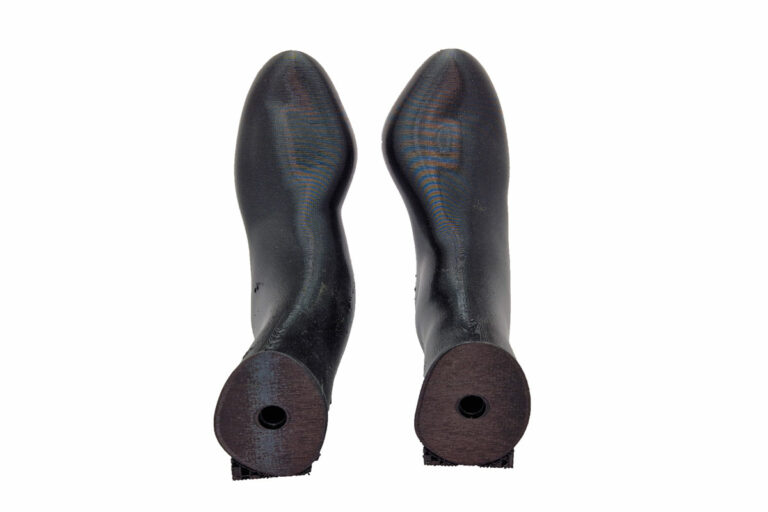
À l’atelier de Breizh Podo, on ne voit pas la 3D comme un gadget
À ce stade, Coline, formier-liégiste à l‘atelier de Breizh Podo, confirme qu’elle ne voit que des intérêts à cette numérisation du process de fabrication des chaussures orthopédiques qui a été engagé dans l’entreprise : « Ça change beaucoup au niveau du poids des formes. Par le passé, j’ai eu des problèmes de tendinites et des problèmes de dos à cause de la manipulation de formes beaucoup plus lourdes. Avec ces formes imprimées en 3D, beaucoup plus légères, mes problèmes ont disparu. » Mais ce n’est pas tout, Coline constate bel et bien « qu’il y a beaucoup moins de solvants de résine dans l’air. »
Les formes imprimées en 3D : un véritable bond en avant
En termes de qualité de la production, Coline souligne que « les formes sont beaucoup plus personnalisées grâce à la chaine 3D de production. Avant, on n’avait pas de formes montantes et on perdait de la précision dans la tige de la chaussure, qu’il fallait souvent reprendre après les premiers essais par le patient (lire la relève de formes). Désormais, le scan de départ permet de bénéficier de tous ces éléments hauts que l’on n‘avait jamais avant, car les moulages s’arrêtaient sous la cheville. Avec ces scans plus complets et précis, le résultat est tout de suite ajusté pour le patient. Le premier essai est souvent le bon ».
Commencer par remplacer le moulage par un relevé 3D
Ce résultat, il a fallu quelques mois et beaucoup d’heures de recherche et de tests pour l’obtenir. C’est en 2021 que notre podo-orthésiste, Luc Sieurin, décide de se pencher sur la question de la modernisation de la production et de sa numérisation. « À un moment, il fallait s’emparer de tous les problèmes que posait le fait de travailler avec des moulages à l’ancienne et il fallait trouver une solution. Il me semblait que les outils numériques devaient être en mesure de répondre à nos besoins. Il était temps de questionner nos façons de faire et de poser les choses à plat. Il fallait trouver le chemin qui nous menait à la solution », résume Luc Sieurin.
Scruter internet et se poser les bonnes questions
Scruter internet et se poser les bonnes questions De façon assez logique, notre technicien s’est appuyé sur les ressources d’internet pour récolter des informations et nourrir sa réflexion.
La première étape a été de trouver la méthode pour la récolte des données de départ. La question du remplacement du moulage « classique » des pieds par un scan digital a été assez rapide à régler. Des outils et logiciels relativement simples et pas trop couteux existaient.
Une fois que la méthode et le matériel nécessaire à réaliser l’image des pieds en 3D ont été validés, une série de questions s’est présentée : que faire avec le fichier 3D des pieds ? Comment réaliser les corrections ? Comment obtenir une forme exploitable et capable de remplacer les moulages ?
Place à la Conception Assistée par Ordinateur (CAO)
Pour « manipuler » le scan 3D, pour lui apporter des corrections et pour ordonner la fabrication d’une forme à une imprimante 3D, il a fallu trouver une solution informatique. Ce trait d’union, on le nomme « conception assistée par ordinateur », que l’on résume par « CAO ». Des logiciels de CAO existent sur le marché. Il fallait donc trouver la solution qui cochait toutes les cases : accessibilité, prise en main, fonctionnalités, coût et résultats…
Plusieurs essais de logiciels de CAO avant d’opter pour Rhino
« J’ai essayé plusieurs logiciels comme SpaceClaim, Fusion 360 et j’ai écarté ceux qui étaient hors de portée financièrement, rappelle Luc Sieurin. Pendant toute cette phase d’exploration et de recherche, j’ai découvert le compte podotools sur YouTube. J’y ai découvert différentes solutions d’usage du logiciel Rhino (Rhinoceros 3D, alias Rhino 8, logiciel de CAO développé par l’entreprise Robert McNeel & Associates) sur la conception des formes. Je connaissais Rhino depuis environ 10 ans. J’ai décidé de creuser cette piste. Un jour, dans une des vidéos, j’ai trouvé un petit bout de code informatique de Grasshoper. Grasshopper est un langage et un environnement de programmation visuelle qui s’exécute dans Rhinoceros 3D. J’ai travaillé sur ce bout de code et j’ai essayé de comprendre comment ça marchait, ce que ça apportait. J’ai fait des essais, puis j’ai orienté mon travail sur le code vers la création d’un programme adapté à mes besoins. J’ai découvert qu’avec Grasshoper je pouvais créer des mesures, des boutons, bref, des fonctions et l’interface dont j’avais besoin. J’ai ainsi obtenu la V1 d’un outil qui me permettait de fabriquer des formes en impression 3D. »
Une V1 améliorée de façon empirique
À partir de cette « V1 » du programme de pilotage de Rhino par Grasshoper, Luc Sieurin poursuit sa quête sur la base d’une recherche empirique. À l’aide d’observations, de recherches et d’analyses qui reposent sur l’étude de faits et de comportements concrets, il avance pas à pas, heure après heure, vers des certitudes tangibles et vers une base sur laquelle il va pouvoir s’appuyer de façon de plus en plus solide.
« J’ai ajouté des informations, j’ai réduit le nombre de clics, j’ai cherché à gagner du temps et à automatiser le plus d’actions possible. J’ai donc passé du temps à coder, puis je créais une forme, puis j’adaptais le code et je recommençais sans cesse. Moule après moule, j’ai essayé de gagner en efficacité et en qualité », résume Luc Sieurin.
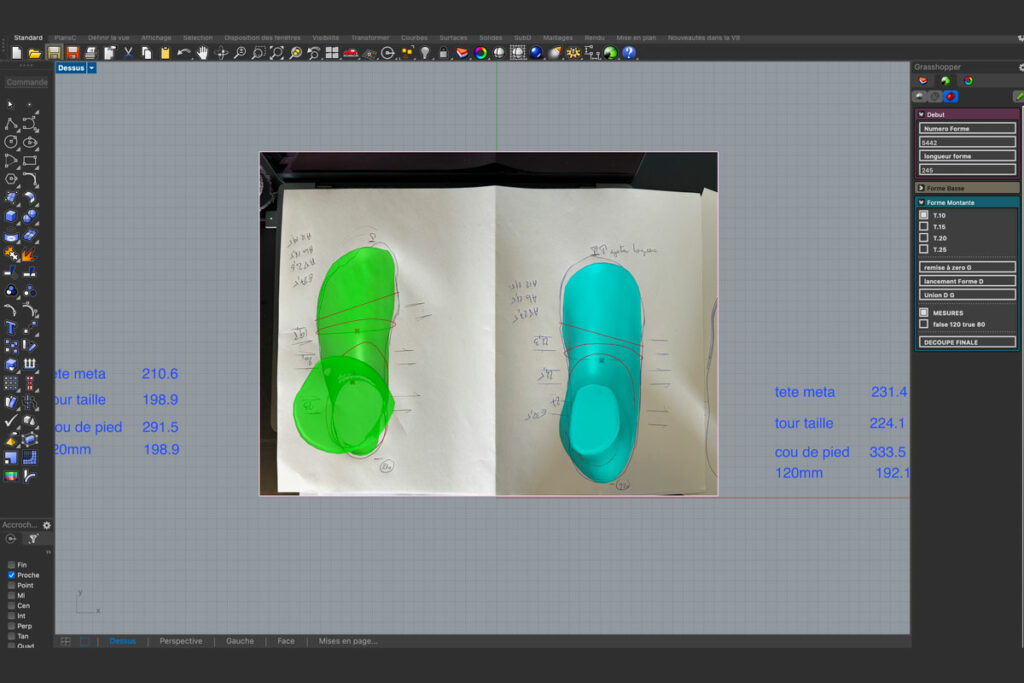
Élargir le champ pour trouver des solutions pour les formes
Le chemin n’a pas été droit et linéaire. Luc Sieurin a parfois dû s’éloigner de sa réflexion au sujet de la production des formes pour y revenir avec des solutions trouvées dans d’autres domaines : « J’ai lancé d’autres chantiers, comme celui de la fabrication des semelles, parce que je bloquais sur les formes. Mon niveau d’apprentissage et de maitrise a augmenté, ce qui m’a permis de revenir ensuite sur le sujet des formes avec des solutions qui me permettaient de dépasser le stade où j’en étais resté. »
Un gros obstacle avant de trouver la solution
À ce stade, Luc sait qu’il a gagné en précision. Il améliore aussi sa maitrise sur les points et les courbes des formes, ou encore sur les points de perforation.
Il connaît néanmoins de véritables trous d’air dans son parcours, à l’image de 6 à 7 mois en 2022 pendant lesquels il est à l’arrêt : « En changeant d’ordinateur, plus rien ne fonctionnait, j’étais dans l’impasse. En septembre 2022, j’ai découvert un plug-in qui m’a permis de tout réimplanter proprement et de repartir de l’avant. Ensuite, fin 2022, j’ai décidé de suivre des formations sur Rhino et début 2023, j’ai passé un cap pour m’approcher du but. Pendant le premier trimestre 2023, j’ai réussi à compléter le code des formes pour aboutir à une version quasi définitive, que je modifie très peu depuis. »
Un pari gagnant pour l’entreprise
« Désormais, dès que j’ai un questionnement ou une recherche, j’ai l’architecture du logiciel dans la tête et je suis en mesure de trouver des solutions. J’ai une solution qui me permet de tout adapter, d’améliorer les choses tout seul, de façon autonome. Au total, je pense avoir passé 300 à 400 heures pour en arriver là », explique Luc Sieurin.
Selon celui qui est aussi le dirigeant de Breizh Podo, cet investissement en temps est d’ores et déjà rentable : « J’ai mobilisé un temps qu’on peut évaluer à environ 10 000 €, mais un logiciel équivalent, qui ne serait pas forcément adapté à mes besoins à 100%, c’est au moins 12 000 €. Chez Breizh Podo, tout le monde manipule désormais des formes beaucoup plus légères. Nous avons des gains en qualité, en précision, en efficacité et en productivité. Le projet était un peu fou, il y avait un risque de perdre du temps, mais aujourd’hui, on sait que c’est un pari qui a été gagnant. En misant un peu de temps, nous avons obtenu des résultats formidables. »
La maitrise des formes 3D, un passeport vers la suite…
Bien entendu, la conception et la réalisation d’une chaussure orthopédique complète ne reposent pas que sur la création de formes. Nous verrons dans les articles suivants en quoi Rhino est intervenu dans le patronage et la relève de formes, dans la conception d’orthèses, puis nous découvrirons que Luc Sieurin et Breizh Podo ont encore de projets à développer. Si vous voulez en savoir plus et découvrir comment nous avons poursuivi notre parcours de numérisation de la production en podo-orthésie, rendez-vous (prochainement) pour le deuxième article de notre série : Rhinoceros 3D. Ep 2/4. Le patronage, la relève de formes.